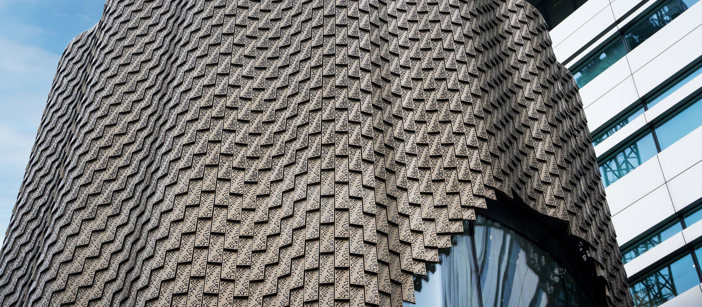
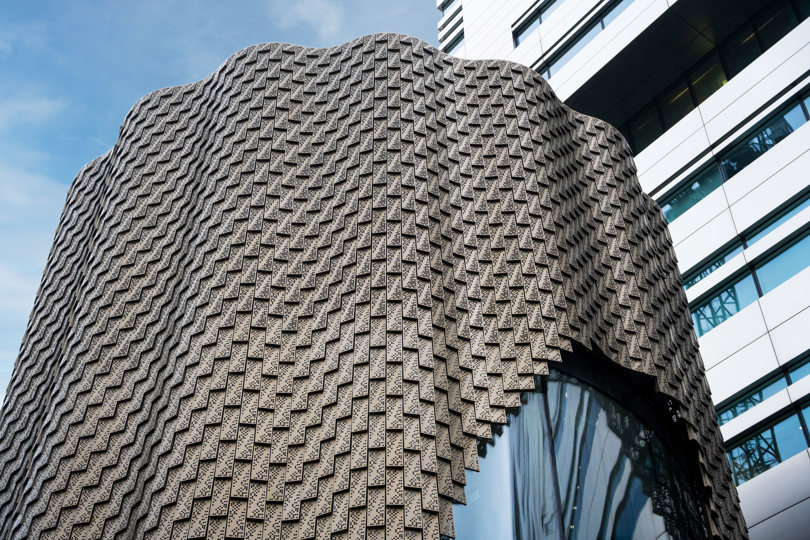
Find out how our VERSA 8006 aluminium solution was a decisive factor in the production of the world's first performance cooler.
Plastic coolers have been known and widely used for over 50 years. They consist of a mixture of polyethylene plastic and polyurethane foam. Neither material is particularly durable, nor can they be easily recycled. When recycling a plastic cooler, the polyurethane foam first has to be laboriously removed from the plastic shell as, unlike the plastic shell, it cannot be melted down. There are also other disadvantages: Conventional cool boxes are heavy and unwieldy and the cooling capacity diminishes considerably after just a few hours.
Ian Sandmæl, co-founder and product designer at Oyster, wanted to develop a modern cool box made from sustainable and recyclable materials that is lightweight and, above all, offers significantly better insulation. He saw the solution for excellent cooling performance in vacuum insulation technology. However, the development and production of a vacuum-insulated cool box for food and drinks posed a number of practical challenges.
The lightest possible material had to be found that met both the technical functionality for vacuum insulation and the aesthetic requirements for the design of the cool box. Only aluminium offered the appropriate material properties and could meet the requirements.
Speira was already involved in the development phase and supported Oyster with its many years of material expertise. Together, various alloys and deep-drawing processes were tested for the manufacturing process in order to find the perfect material solution for the realization of the cool box. To enable vacuum insulation in a square shape, the insulation system was to be made from a 1 mm thick aluminium sheet. After several tests and simulations, our VERSA 8006 aluminium solution was chosen, as this alloy is able to withstand the compression and expansion forces that occur during deep drawing. It also ensures correct geometry and the necessary strength to prevent breakage under the influence of vacuum pressure.
In addition to the excellent deep drawing properties of VERSA 8006, aluminium offers outstanding thermal properties and an impermeable barrier. The high thermal conductivity ensures that the temperature is distributed evenly and quickly across the inner wall surfaces of the cool box. Compared to plastic coolers, there is no need for large quantities of loose ice cubes. Filling with cold drinks and small ice packs is sufficient to keep the inside of the cool box cold for many hours. Even after 24 hours, the temperature inside the box is less than 5 degrees Celsius. The storage tray and lid form a hermetically sealed vacuum chamber. The aluminium shell encloses the chambers as an impermeable barrier, protecting them from the penetration of gases and thus maintaining the vacuum permanently. Aluminium is one of the few materials that can guarantee this.
The use of aluminium also makes it possible to reduce the wall thickness and achieve a space-saving design. The aluminium cool box not only gets cold faster, it also stays cold for longer and offers more space for drinks and food. The Oyster cooler can transport up to 36 beverage cans.
In addition to the aesthetically modern design thanks to the bare aluminium surface, the material also scores highly in terms of durability and robustness. In everyday life and when traveling, the material can withstand a few dents and scratches without impairing the function of the cooler. The box is also designed so that each part can be easily replaced and repaired. And if a cooler does become end-of-life, the aluminium remains a valuable raw material. Another advantage of aluminium over plastic is its high recyclability. Aluminium is melted down and returned to the cycle. The Oyster Tempo Cooler is the first cooler that can be completely recycled.
After six years of development, Oyster has succeeded in developing an aluminium cooler that offers a perfect balance between space, weight, robustness and thermal performance. For the Oyster Tempo Cooler, Speira has since supplied rolled aluminium of the material type VERSA 8006 in consistently high quality. Watch the video and see for yourself how our alloy is a game changer for construction and design.
Our team is always at your side. Feel free to contact us with your next project, your questions and ideas - and let us shape the future together as partners. You can reach us via our contact form. We look forward to hearing from you.