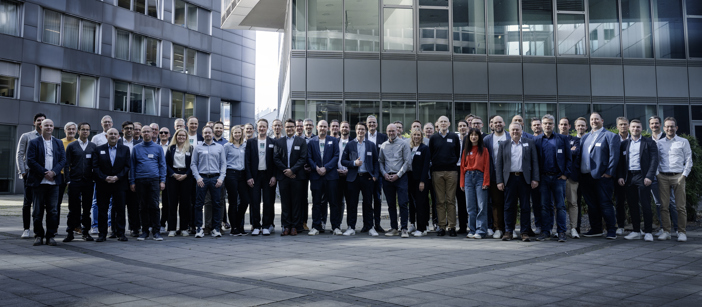
Speira has reached another milestone in its sustainability journey: As part of the EU-funded HyInHeat project, the aluminium recycling and rolling group has successfully converted a melting furnace with a capacity of 1.5 tonnes to hydrogen operation. Initial tests at Speira’s R&D Center in Bonn with various scrap types show promising results with no impact on melt quality.
Hydrogen: A key to decarbonisation
“Sustainability is central to Speira’s mission,” says Dr Paula Camean Queijo, Head of Research and Development at Speira. “While we already rely heavily on recycling to lower our carbon footprint, the use of hydrogen allows us to make the production process itself more environmentally friendly.”
Launched in 2023, the HyInHeat project brings together 30 partners from twelve European countries to explore hydrogen’s potential for decarbonising heat-intensive processes in the aluminium and steel industries. With €24 million in funding from the European Union, the initiative aims to develop efficient hydrogen combustion systems that address nearly the entire process chain of these energy-intensive industries.
Promising test results
Initial tests of the retrofitted a 1.5-tonne capacity furnace using various types of aluminium scrap demonstrated that the quality of the melted metal remains consistently high: “Our early trials have been very encouraging,” reports Galyna Laptyeva, Senior Scientist and Project Lead at Speira. “We’ve proven that hydrogen is fundamentally suitable as a fuel for our melting furnaces. This is a major step towards reducing the carbon intensity of our production.”
Driving innovation through research and development
To further increase efficiency, Speira has now equipped the test furnace with even more advanced technology. Instead of using normal air, hydrogen is now burned with pure oxygen – a process known as "oxyfuel."
“Oxygen is a by-product of hydrogen production anyway. By using it for combustion, our calculations show we can save approximately 30 per cent of fuel,” explains Laptyeva. “This makes the process not only more environmentally friendly but also more economical.”
Another advantage of hydrogen combustion is that, ideally, no harmful nitrogen oxides (NOx) are produced. In practice, however, small leaks and impurities can cause minimal amounts of these pollutants. Researchers will closely examine how to reduce these emissions to a minimum in upcoming tests.
“Our commitment to research and development is an essential component of our sustainability strategy,” emphasises Camean Queijo. “With projects like HyInHeat, we are pioneering a more environmentally friendly aluminium industry while strengthening Germany’s position as an innovation hub.”
With the successful conversion of the melting furnace to hydrogen operation, Speira has made an important contribution to researching low-emission production processes. The results from the HyInHeat project are intended not only to advance the company's own operations but also to provide new approaches for more sustainable production across the entire industry.
About HyInHeat:
HyInHeat is a European funded project that aims to integrate hydrogen as a fuel for high-temperature heating processes in energy-intensive industries, particularly in the aluminium and steel sectors. The project seeks to reduce carbon dioxide emissions from these sectors by implementing efficient hydrogen combustion systems that cover almost their entire process chains.
The HyInHeat consortium is a diverse and collaborative group of 30 partners from twelve European countries, united in their goal to develop and demonstrate innovative hydrogen-based heating technologies for energy-intensive industries. Together, they bring expertise in various fields related to industrial heating, including combustion, furnaces, sensors, safety and sustainability. The consortium includes leading research institutes, companies providing technology and equipment, and industrial companies from the aluminium and steel sectors, with an additional focus on exploitation and dissemination activities.
The project will run until the end of 2026 and is being coordinated by the Department for Industrial Furnaces and Heat Engineering (IOB) at RWTH Aachen University.
Check out hyinheat.eu for more information.